In Læsø, houses are roofed with thick and heavy bundles of seaweed that could become the ideal building material for the rest of the world to “imitate”.
On most summer days on the Danish island of Læsø, you’ll find a man named Henning Johansen hard at work. Johansen is a native of the island. His job is… a roofer. But on Læsø, the job of a roofer is unlike any other in the world.
Necessity is the mother of invention
Located 19km off the northeast coast of Jutland, the island of Læsø appears in Norse mythology as the home of the giant Ægir, and is famous for its shipwrecks, which are mentioned throughout Danish naval history. However, the most unique feature of Læsø is the houses on it.
The houses can be considered unique in the world, because they are roofed with thick and heavy bundles of seaweed.
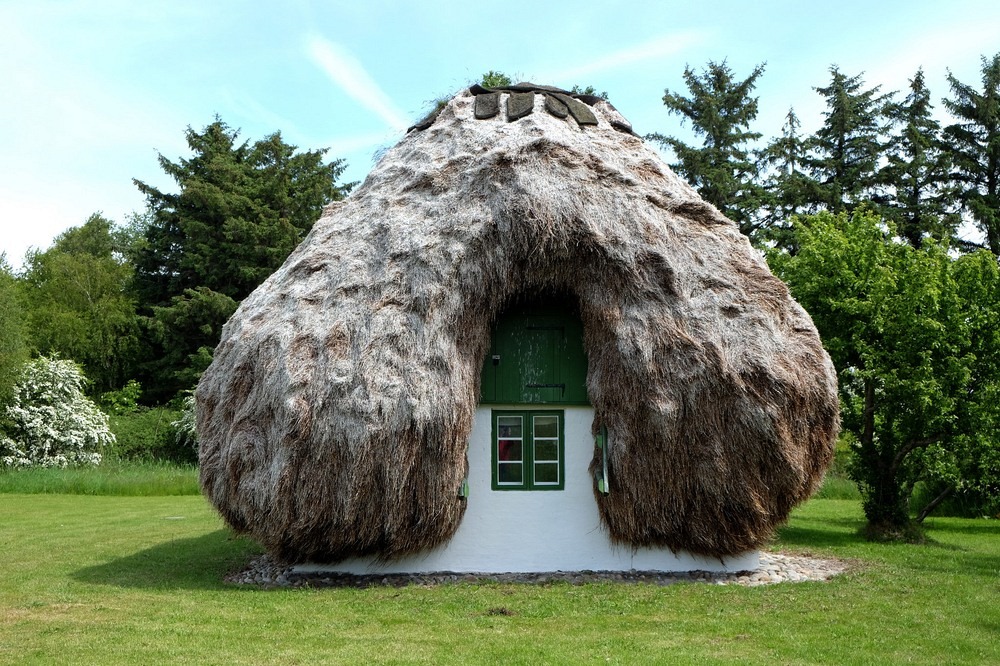
On the island of Læsø, off the coast of Denmark, there are houses thatched with seaweed.
Seaweed thatching began on Læsø in the 17th century and was unique to that island. Later, seaweed roofs were said to have been seen on Scotland’s Orkney Islands.
And this habit was not a spontaneous invention, but simply a matter of “necessity is the mother of invention” for the local people. Because Læsø, home to a thriving salt industry, had been deforested – the trees were burned to provide energy for the salt mines. So the islanders needed to find an alternative roofing material. The island itself had few resources and was mostly mudflats and sandbanks, making farming difficult. So the people turned to the sea.
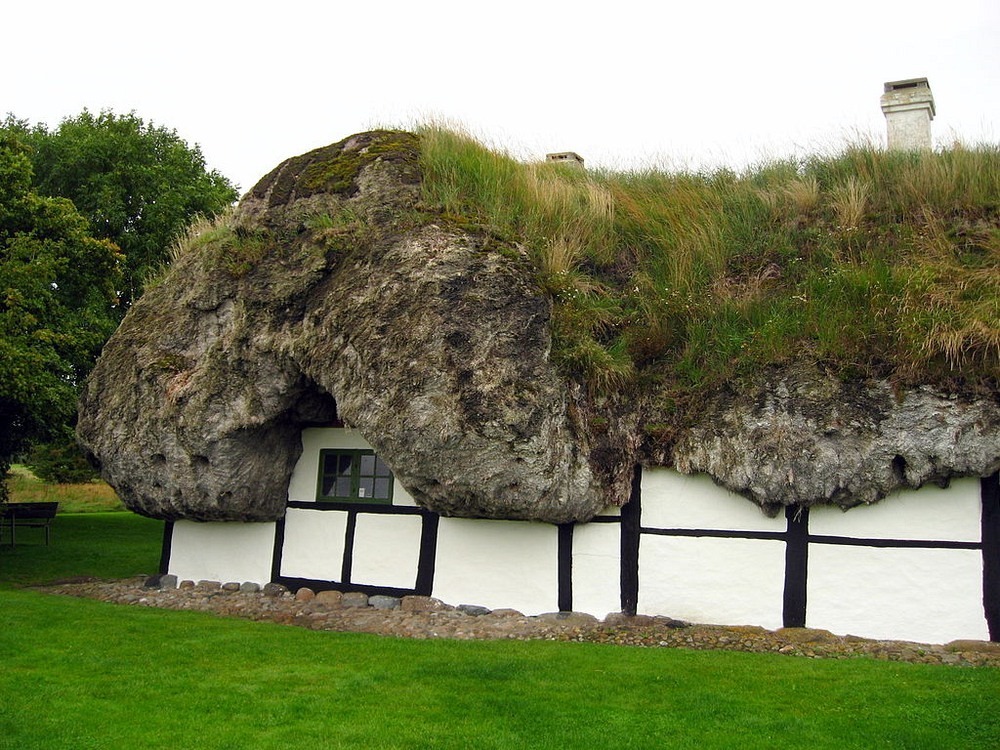
Apart from their enormous size, they look a lot like thatched roofs. Some of these roofs are over 300 years old. They are unique to the island of Læsø.
People used driftwood from sunken ships offshore to make the house frame and seaweed called zostera marina (also known as eelgrass) dragged from the shore to make the roof.
By the early 20th century, most houses on Læsø were thatched with seaweed. However, after a fungal disease wiped out much of the zostera marina seaweed in the 1920s, knowledge of this roofing technique gradually disappeared. There were then just 36 seaweed-thatched houses left on the island of 1,800 people.
Reviving a priceless heritage
Since 2012, Mr. Henning Johansen has been reviving this technique when repairing roofs. He is considered a pioneer in the seaweed roofing technique.
“It’s one of the biggest things in Læsø’s history, so it’s very important for the island,” Mr Johansen told BB Travel while working on the roof.
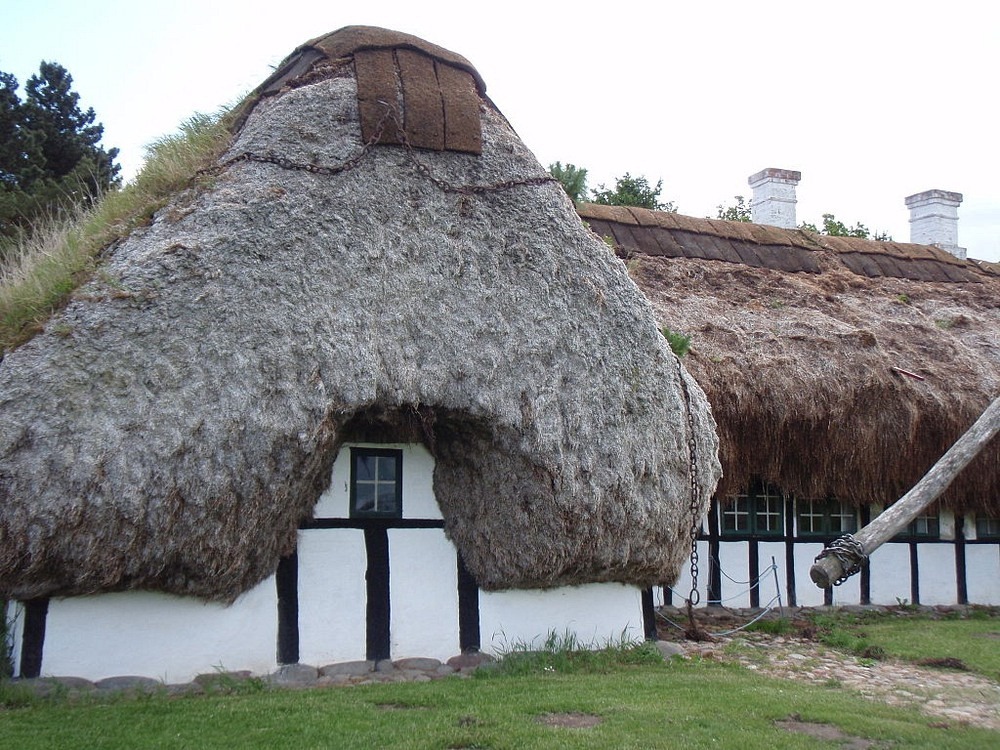
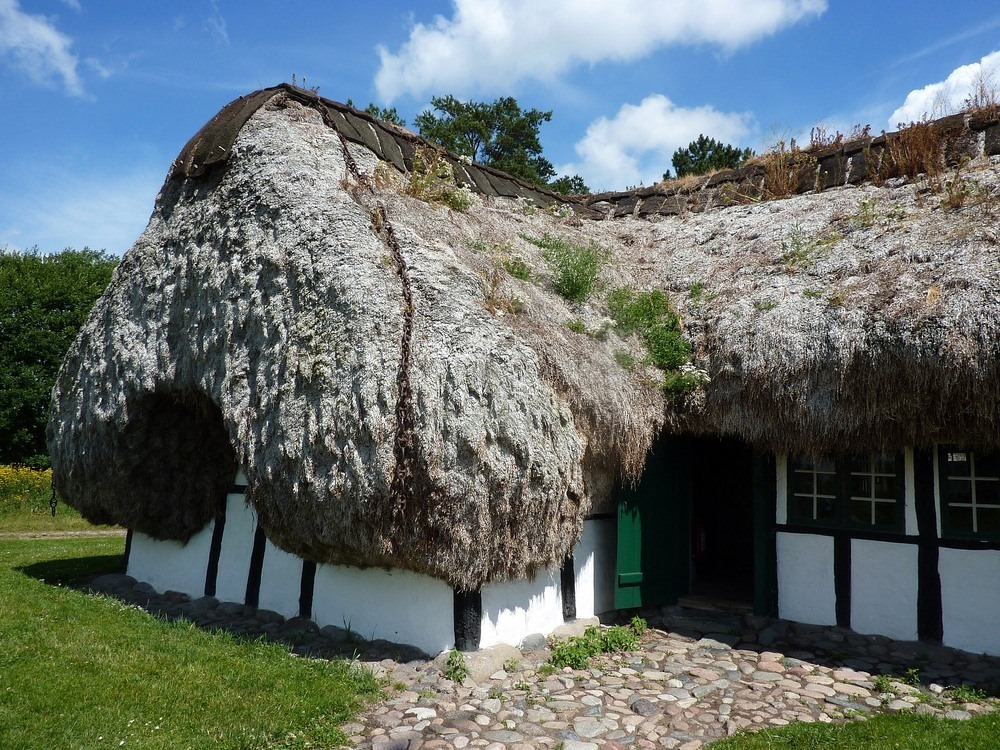
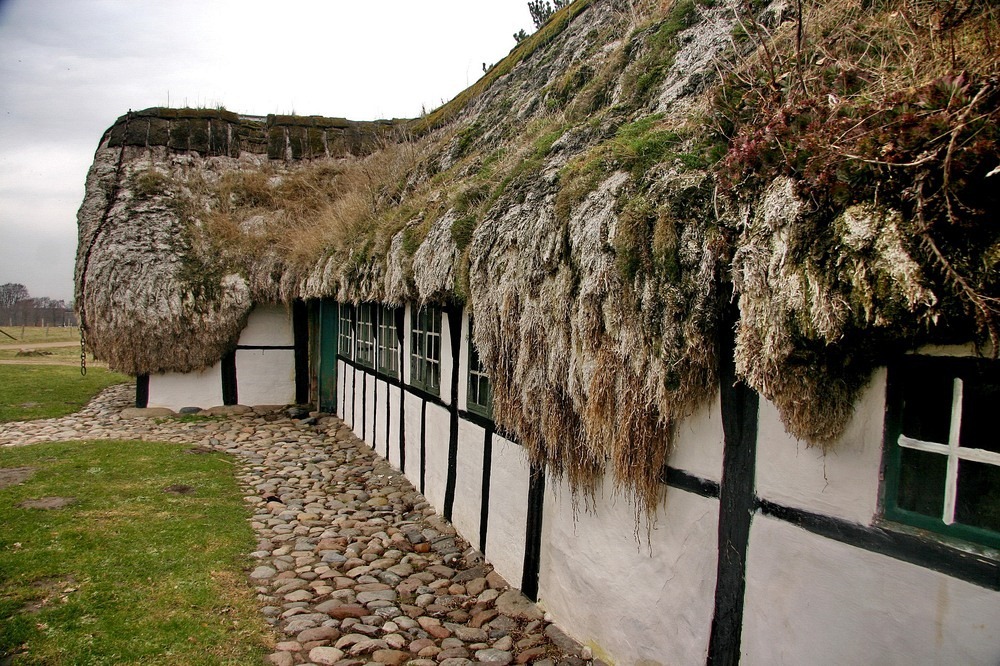
“This was traditionally women’s work,” he added, explaining: “Because the men on the island were often out at sea, the women had to look after the farms and homes. They were alone on this island and looked after themselves. They figured out how to make these roofs, which is something that has never been seen anywhere else in the world. So of course we are very proud of our heritage.”
About 40 to 50 women work together on the roof. They collect seaweed after autumn storms, then spread it out in the fields to dry for about six months, which removes microalgae and prevents the seaweed from rotting.
When construction began, they treated the seaweed as if it were wool, twisting it into large ropes and tying them to the rafters to act as supports. Layers of seaweed were then piled on top and weighed down with peat: the average roof was over a meter thick and weighed between 35 and 40 tons.
Once the roofing work was complete, the women would place chairs on it to sit and look out to sea, looking for shipwrecks (to see if they could salvage the wrecks) and walk around, even dancing on the seaweed roof to compact it.
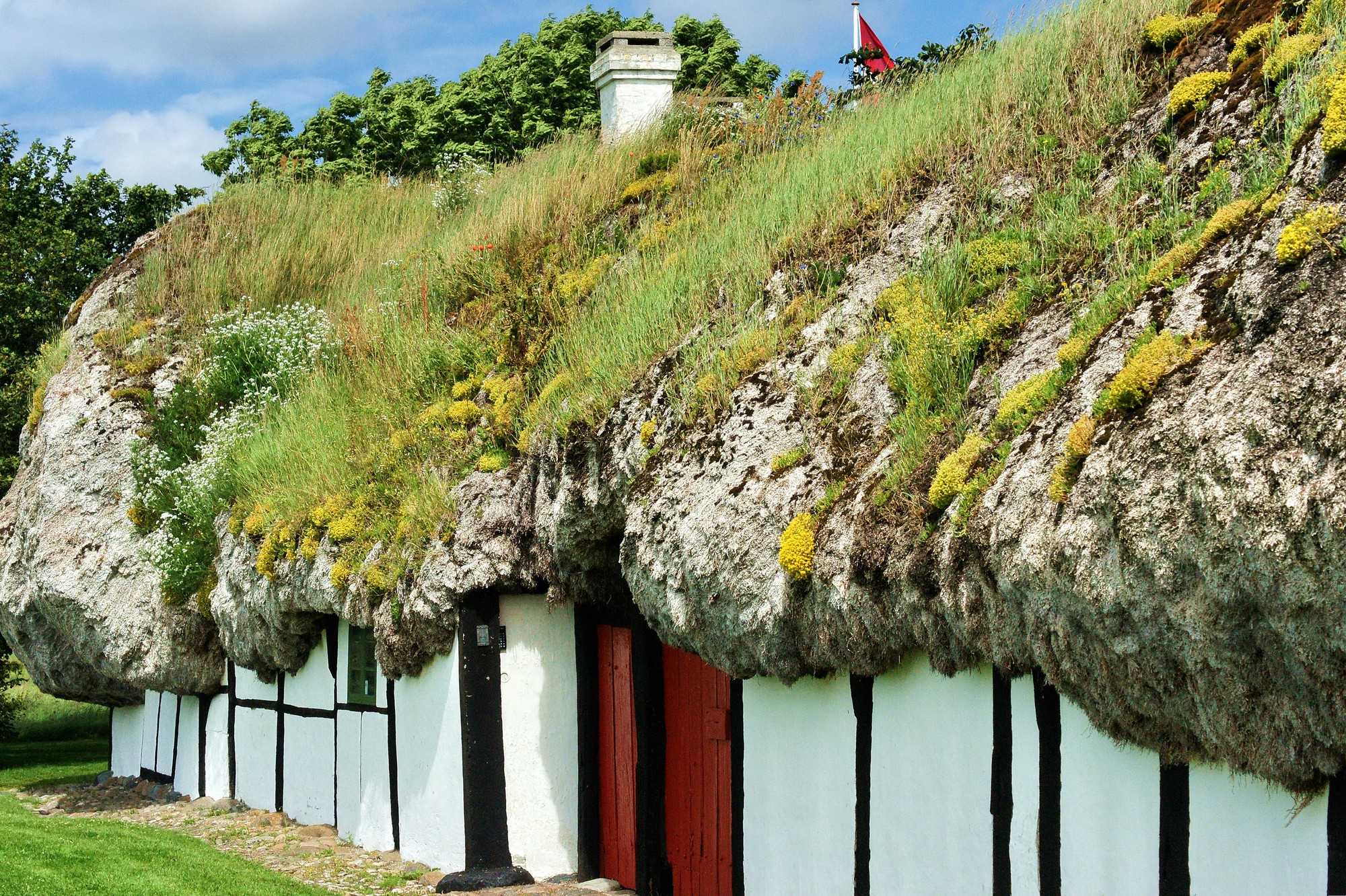
Because the eelgrass is salt-soaked, the roof does not rot easily and can last for hundreds of years.
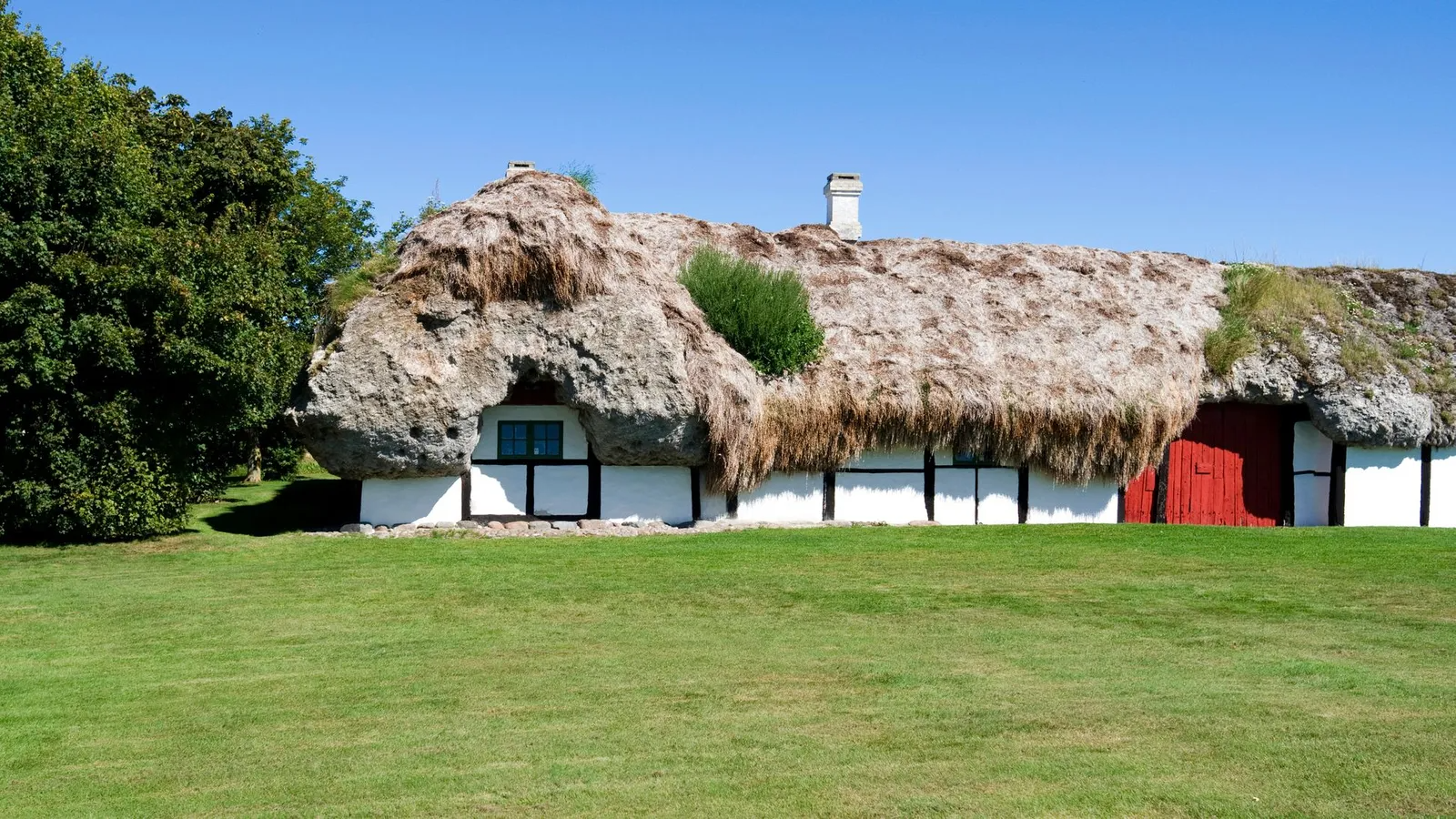
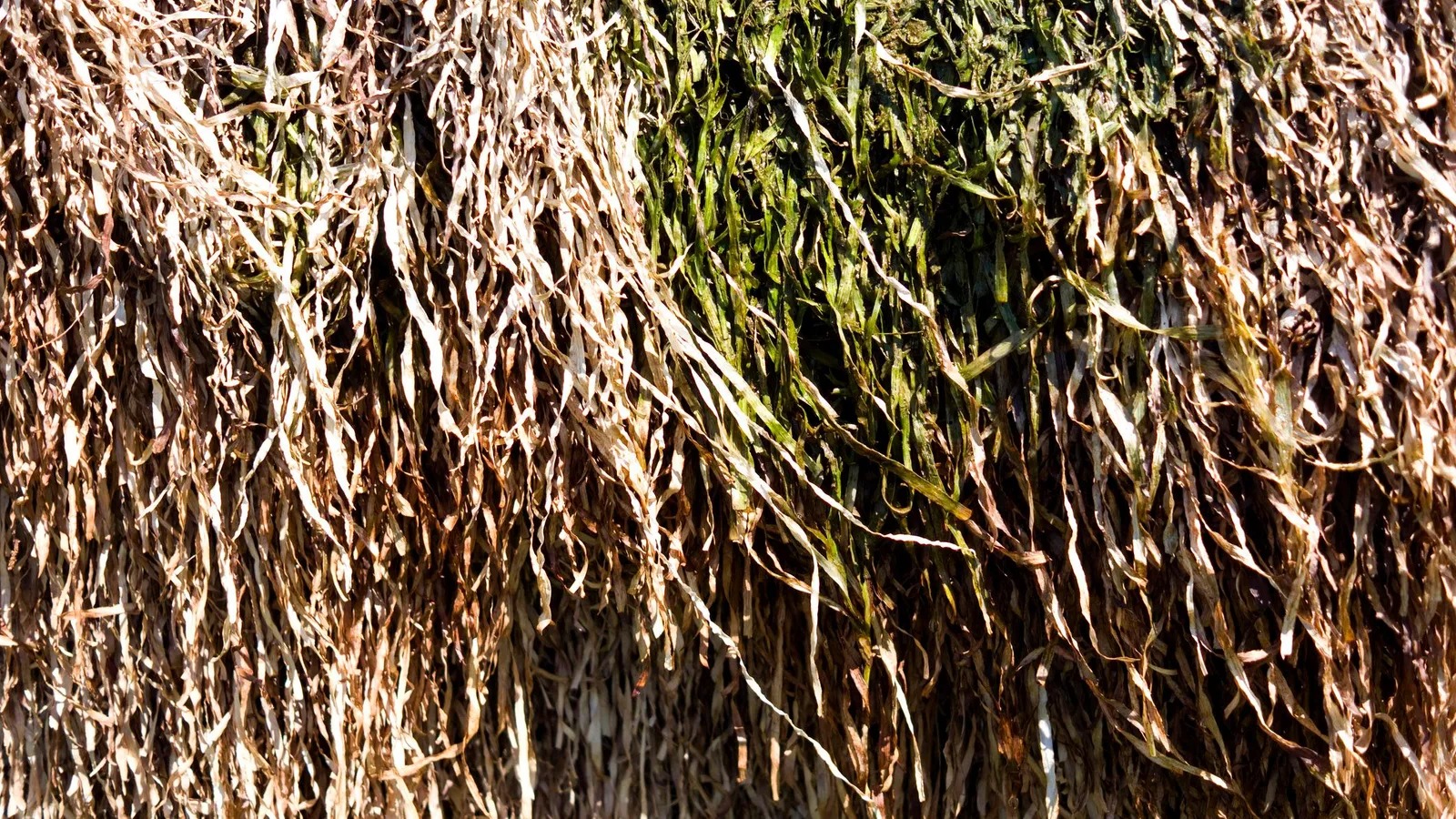
Eelgrass grows in the sea off the island and was once so abundant that it regularly washed ashore. It has long, bright green, ribbon-like leaves, about a centimeter wide and up to 2 meters long.
Johansen says they can do a roof in a day. For his local team of five roofers, it takes about 21 hours. “Because I don’t have enough manpower, which is 50 women.”
But it’s not just for heritage purposes that Johansen is reviving seaweed thatching. “Eelgrass is a very interesting material,” he says, “because it doesn’t burn easily because it’s so salty inside.”
Eelgrass, commonly known as “seaweed,” has long leaves that can grow up to 2m in length. It is found all over the world, although mostly in the northern hemisphere. Not only is eelgrass naturally resistant to fire, rot and pests, it also absorbs CO2.
Farmers collect the grass from the beach and after drying, they bundle it and twist it into thick ropes, which are then woven through the rafters of a house to form the roof.
After about a year, eelgrass will be completely waterproof and have insulating properties comparable to mineral wool, a dense, fibrous material made from molten glass, rock or industrial waste.
A roof made from this seaweed can last for hundreds of years. One of the surviving seaweed roofs on the island of Læsø is over 300 years old. In comparison, tile roofs typically last only about 50 years.
This combination of sustainability and heritage caught the attention of Copenhagen-based American architect Kathryn Larsen, who is currently researching how Læsø’s traditional seaweed roofing can be updated into a sustainable contemporary building material around the world.
While studying at the KEA School of Design and Technology in Copenhagen, Larsen focused his thesis on seaweed roofs on the island of Læsø, a topic with very few English-language resources.
“It became a big mystery to me because most of the information was in Danish,” she said. “I was really fascinated by it for a few years. I was determined to learn more Danish and then research the subject further. It really became a passion of mine.”
Larsen wants to change the way the construction industry looks at old techniques that are “not only good for the environment by using naturally renewable resources, but also create buildings that are friendly to people.
Because eelgrass grows all over the world, Larsen sees huge global potential for its use as a sustainable building material.
On Læsø, Johansen still has 10 more roofs to replace. It’s a long-term project, but he says he doesn’t want to rush it “because it’s much easier to tell tourists about the island’s history when people come and see me repairing old houses.”
Visitors to Læsø are invited to watch Mr Johansen work on weekdays during the summer, where they can see first-hand “how seaweed roofs work, what they look like and how interesting they are”.
Eelgrass is part of the world heritage, says Johansen. “You can come to Læsø and I can show you the history because it was used extensively all over the world – everywhere from the Dutch Wadden Sea, where it was used to build sea walls, to New England, where houses were insulated with Cabot’s Quilt, a thermal and acoustic insulator made from dried eelgrass.
“Seaweed roofs have a monumental history, which was very quickly forgotten and now I am starting to tell it again,” said Mr Johansen.